20,000 டன் கூட்டு உரங்களின் வருடாந்திர உற்பத்தி வரிசையானது மேம்பட்ட உபகரணங்களின் கலவையாகும்.குறைந்த உற்பத்தி செலவு மற்றும் அதிக உற்பத்தி திறன்.பல்வேறு கலப்பு மூலப்பொருட்களின் கிரானுலேஷனுக்கு கலவை உர உற்பத்தி வரியைப் பயன்படுத்தலாம்.இறுதியாக, வெவ்வேறு செறிவுகள் மற்றும் சூத்திரங்கள் கொண்ட கலவை உரங்களை உண்மையான தேவைகளுக்கு ஏற்ப தயார் செய்து, பயிர்களுக்குத் தேவையான ஊட்டச்சத்துக்களை திறம்பட நிரப்பி, பயிர் தேவைக்கும் மண் வழங்கலுக்கும் இடையே உள்ள முரண்பாட்டைத் தீர்க்கலாம்.
கலப்பு உர உற்பத்தி வரிசையில் பல்வேறு பயிர்களுக்கு அதிக, நடுத்தர மற்றும் குறைந்த செறிவூட்டப்பட்ட கலவை உரங்களை உற்பத்தி செய்யலாம்.சிறிய முதலீடு மற்றும் குறைந்த ஆற்றல் நுகர்வுடன் உற்பத்தி வரி வறண்டதாக இருக்க வேண்டியதில்லை.
கலப்பு உர உற்பத்தி வரிசையின் உருளையானது வெவ்வேறு அளவுகளின் துகள்களை கசக்கி உற்பத்தி செய்வதற்கு வெவ்வேறு வடிவங்கள் மற்றும் அளவுகளில் வடிவமைக்கப்படலாம்.
பொதுவாக, கலவை உரத்தில் குறைந்தது இரண்டு அல்லது மூன்று ஊட்டச்சத்துக்கள் (நைட்ரஜன், பாஸ்பரஸ், பொட்டாசியம்) உள்ளன.இது அதிக ஊட்டச்சத்து உள்ளடக்கம் மற்றும் சில பக்க விளைவுகளைக் கொண்டுள்ளது.சமச்சீர் உரமிடுவதில் கூட்டு உரம் முக்கிய பங்கு வகிக்கிறது.இது உரமிடுதல் திறனை மேம்படுத்துவது மட்டுமல்லாமல், பயிர்களின் நிலையான மற்றும் அதிக மகசூலை ஊக்குவிக்கும்.
உர உற்பத்தி வரிசை உபகரணங்களின் தொழில்முறை உற்பத்தியாளராக, நாங்கள் வாடிக்கையாளர்களுக்கு உற்பத்தி உபகரணங்களை வழங்குகிறோம் மற்றும் வருடத்திற்கு 10,000 டன்கள் முதல் வருடத்திற்கு 200,000 டன்கள் வரை வெவ்வேறு உற்பத்தி திறன் தேவைகளுக்கு மிகவும் பொருத்தமான தீர்வுகளை வழங்குகிறோம்.
கலவை உர உற்பத்திக்கான மூலப்பொருட்களில் யூரியா, அம்மோனியம் குளோரைடு, அம்மோனியம் சல்பேட், திரவ அம்மோனியா, அம்மோனியம் மோனோபாஸ்பேட், டைஅமோனியம் பாஸ்பேட், பொட்டாசியம் குளோரைடு, பொட்டாசியம் சல்பேட், சில களிமண் மற்றும் பிற கலப்படங்கள் அடங்கும்.
1) நைட்ரஜன் உரங்கள்: அம்மோனியம் குளோரைடு, அம்மோனியம் சல்பேட், அம்மோனியம் தியோ, யூரியா, கால்சியம் நைட்ரேட் போன்றவை.
2) பொட்டாசியம் உரங்கள்: பொட்டாசியம் சல்பேட், புல் மற்றும் சாம்பல் போன்றவை.
3) பாஸ்பரஸ் உரங்கள்: கால்சியம் பெர்பாஸ்பேட், கனமான கால்சியம் பெர்பாஸ்பேட், கால்சியம் மெக்னீசியம் மற்றும் பாஸ்பேட் உரம், பாஸ்பேட் தாது தூள் போன்றவை.
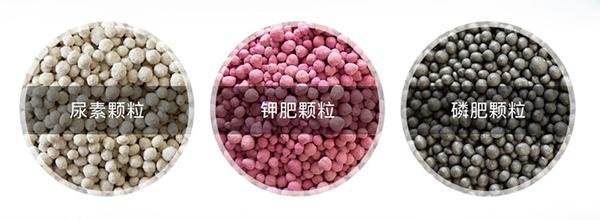
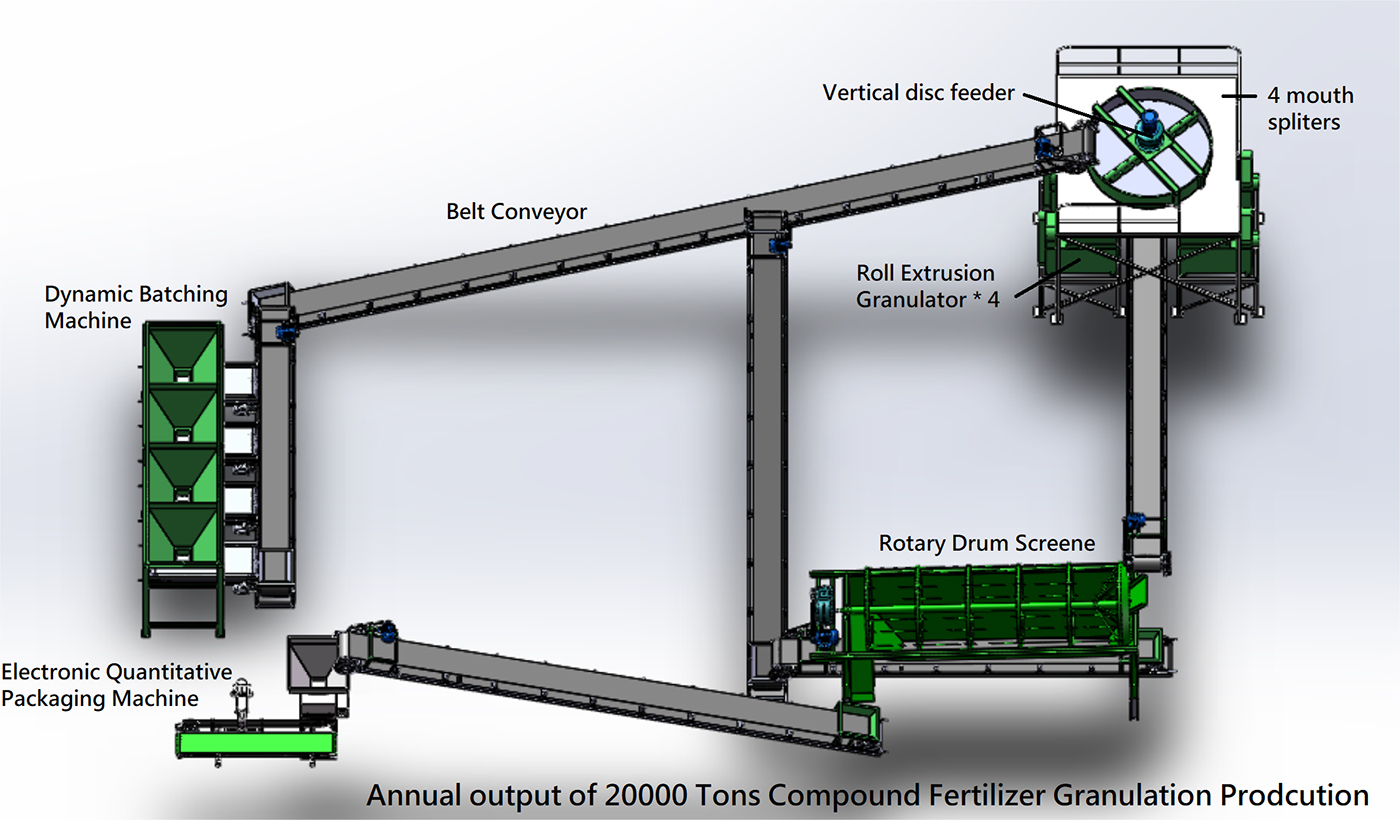
1.கலப்பு உர உற்பத்தி வரி குறைந்த ஆற்றல் நுகர்வு, பெரிய உற்பத்தி திறன் மற்றும் நல்ல பொருளாதார நன்மைகள் ஆகியவற்றின் பண்புகளைக் கொண்டுள்ளது.
2. உற்பத்தி வரி உலர் கிரானுலேஷனை ஏற்றுக்கொள்கிறது, உலர்த்தும் குளிரூட்டும் செயல்முறையை நீக்குகிறது மற்றும் உபகரணங்களின் விலை உள்ளீட்டை வெகுவாகக் குறைக்கிறது.
3. கலவை உர உற்பத்தி வரி சிறிய மற்றும் நியாயமான, ஒரு சிறிய பகுதியை உள்ளடக்கியது.
4. உற்பத்தி செயல்பாட்டில், சிறிய ஆற்றல் நுகர்வு மற்றும் மூன்று கழிவுகள் இல்லை.கலப்பு உர உற்பத்தி வரிசையில் நிலையான செயல்திறன், நம்பகமான தரம் மற்றும் நீண்ட சேவை வாழ்க்கை உள்ளது.
5. கலவை உர உற்பத்தி வரி பல்வேறு கலவை உர மூலப்பொருட்களை உற்பத்தி செய்ய பயன்படுத்தப்படலாம்.மற்றும் கிரானுலேஷன் வீதம் போதுமான அளவு அதிகமாக உள்ளது.
6. கலவை உர உற்பத்தி வரியானது வெவ்வேறு வாடிக்கையாளர்களின் தேவைகளைப் பூர்த்தி செய்வதற்காக வெவ்வேறு செறிவுகளில் கலவை உரங்களை உற்பத்தி செய்ய முடியும்.
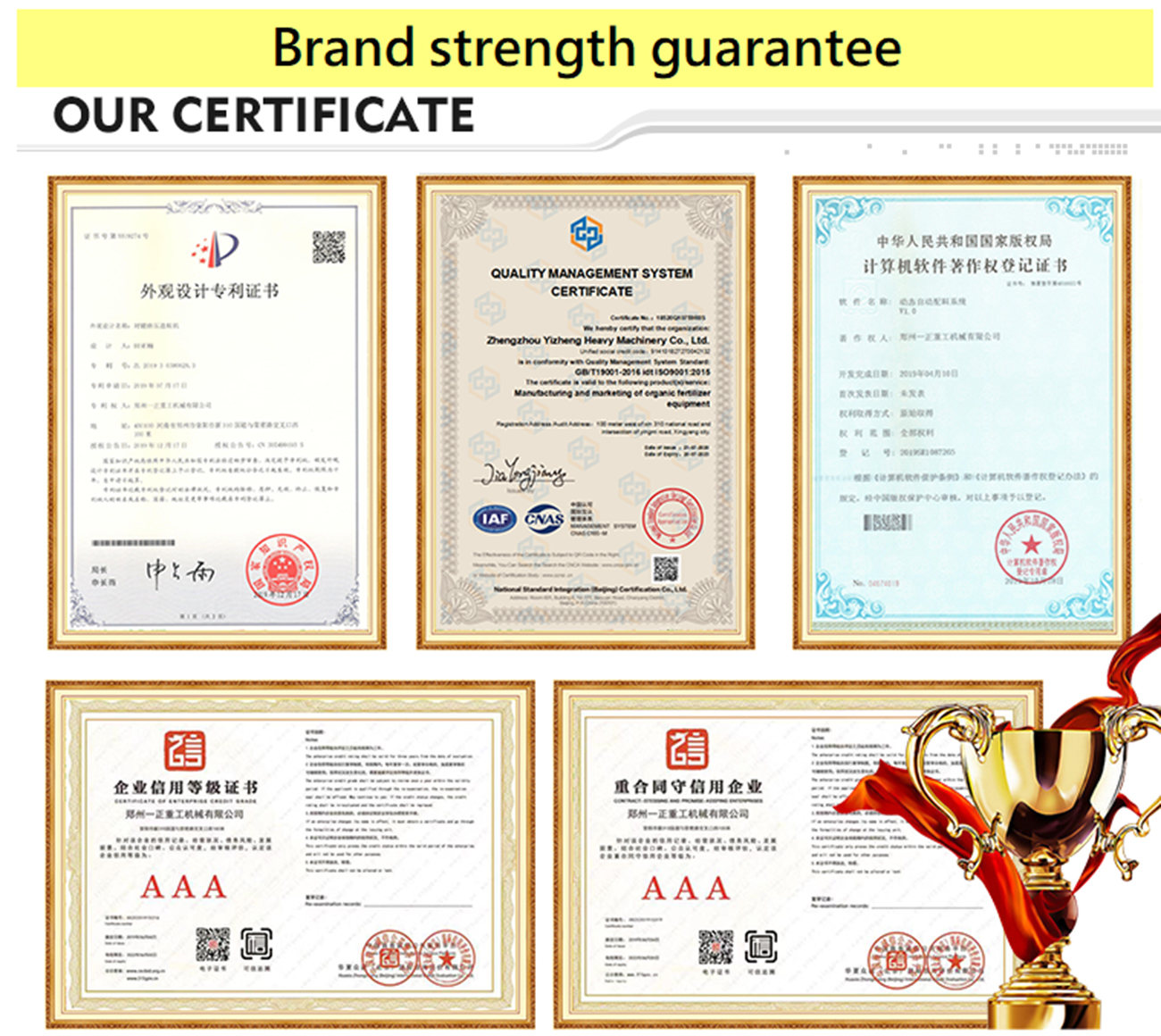
பொதுவாக, கலப்பு உர உற்பத்தி வரிசையில் பொதுவாக பின்வரும் பகுதிகள் உள்ளன: கலவை செயல்முறை, கிரானுலேஷன் செயல்முறை, நசுக்கும் செயல்முறை, திரையிடல் செயல்முறை, பூச்சு செயல்முறை மற்றும் பேக்கேஜிங் செயல்முறை.
1. டைனமிக் பேச்சிங் மெஷின்:
மூன்றுக்கும் மேற்பட்ட பொருட்களின் பொருட்கள் மேற்கொள்ளப்படலாம்.பேட்ச் இயந்திரம் மூன்றுக்கும் மேற்பட்ட சிலோகளைக் கொண்டுள்ளது, மேலும் வாடிக்கையாளரின் தேவைகளுக்கு ஏற்ப சிலோவை சரியான முறையில் அதிகரிக்கவும் குறைக்கவும் முடியும்.ஒவ்வொரு சிலோவின் வெளியேறும் இடத்திலும், ஒரு நியூமேடிக் எலக்ட்ரானிக் கதவு உள்ளது.சிலோவின் கீழ், இது ஒரு ஹாப்பர் என்று அழைக்கப்படுகிறது, அதாவது ஹாப்பரின் அடிப்பகுதி ஒரு பெல்ட் கன்வேயர் ஆகும்.டிரான்ஸ்மிஷன் லீவரின் ஒரு முனையில் ஹாப்பர் மற்றும் பெல்ட் கன்வேயர் தொங்கவிடப்பட்டுள்ளதாகவும், லீவரின் மறுமுனை டென்ஷன் சென்சாருடன் இணைக்கப்பட்டுள்ளதாகவும், சென்சார் மற்றும் நியூமேடிக் கண்ட்ரோல் பகுதி கணினியுடன் இணைக்கப்பட்டுள்ளதாகவும் கூறப்படுகிறது.இந்த இயந்திரம் எலக்ட்ரானிக் செதில்களின் ஒட்டுமொத்த எடையை ஏற்றுக்கொள்கிறது, இது பேட்சிங் கன்ட்ரோலரால் தானாகவே கட்டுப்படுத்தப்படுகிறது, மேலும் ஒவ்வொரு பொருளின் எடை விகிதமும் நிறைவடைகிறது.இது எளிமையான அமைப்பு, உயர் மூலப்பொருள் துல்லியம், எளிமையான செயல்பாடு மற்றும் நம்பகமான பயன்பாடு ஆகியவற்றின் நன்மைகளைக் கொண்டுள்ளது.
2. செங்குத்து சங்கிலி நொறுக்கி:
வெவ்வேறு கலப்பு பொருட்களை ஒரு குறிப்பிட்ட விகிதத்தில் இணைத்து, செங்குத்து சங்கிலி நொறுக்கியில் வைக்கவும்.அடுத்தடுத்த கிரானுலேஷன் செயல்முறையின் தேவைகளைப் பூர்த்தி செய்ய மூலப்பொருட்கள் சிறிய துகள்களாக நசுக்கப்படும்.
3. செங்குத்து வட்டு ஊட்டி:
மூலப்பொருள் நசுக்கப்பட்ட பிறகு, அது செங்குத்து வட்டு ஊட்டிக்கு அனுப்பப்படுகிறது, மேலும் மூலப்பொருள் கலக்கப்பட்டு மிக்சியில் சமமாக கலக்கப்படுகிறது.கலவையின் உள் புறணி பாலிப்ரோப்பிலீன் அல்லது துருப்பிடிக்காத எஃகு தகடு ஆகும்.அதிக அரிப்பு மற்றும் பாகுத்தன்மை கொண்ட இத்தகைய மூலப்பொருட்களை ஒட்டிக்கொள்வது எளிதானது அல்ல.கலப்பு பொருள் டிரம் கிரானுலேட்டரில் நுழையும்.
4. ரோல் எக்ஸ்ட்ரூஷன் கிரானுலேட்டர்:
உலர் வெளியேற்ற தொழில்நுட்பத்தை ஏற்றுக்கொள்வது, உலர்த்தும் செயல்முறை தவிர்க்கப்பட்டது.இது முக்கியமாக வெளிப்புற அழுத்தத்தை நம்பியுள்ளது, இதனால் பொருள் இரண்டு தலைகீழ் ரோலர் அனுமதிகள் மூலம் துண்டுகளாக சுருக்கப்பட வேண்டிய கட்டாயத்தில் உள்ளது.பொருளின் உண்மையான அடர்த்தி 1.5-3 மடங்கு அதிகரிக்கலாம், இதனால் ஒரு குறிப்பிட்ட வலிமை தரத்தை அடைகிறது.தயாரிப்பு ஸ்டாக் எடையை அதிகரிக்க இடங்களுக்கு குறிப்பாக பொருத்தமானது.செயல்பாட்டு நெகிழ்ச்சி மற்றும் பரவலான தழுவல் திரவ அழுத்தத்தால் சரிசெய்யப்படலாம்.உபகரணங்கள் அறிவியல் மற்றும் கட்டமைப்பில் நியாயமானவை மட்டுமல்ல, சிறிய முதலீடு, விரைவான தாக்கம் மற்றும் நல்ல பொருளாதார நன்மைகளையும் கொண்டுள்ளது.
5. ரோட்டரி டிரம் திரை:
மறுசுழற்சி செய்யப்பட்ட பொருட்களிலிருந்து முடிக்கப்பட்ட பொருளைப் பிரிக்க இது முக்கியமாகப் பயன்படுத்தப்படுகிறது.சல்லடைக்குப் பிறகு, தகுதிவாய்ந்த துகள்கள் ரேப்பர் இயந்திரத்தில் செலுத்தப்படுகின்றன, மேலும் தகுதியற்ற துகள்கள் செங்குத்து சங்கிலி நொறுக்கிக்குள் செலுத்தப்பட்டு மீண்டும் கிரானுலேட் செய்யப்படுகின்றன, இதனால் தயாரிப்பு வகைப்பாடு மற்றும் முடிக்கப்பட்ட பொருட்களின் சீரான வகைப்பாடு உணரப்படுகிறது.இயந்திரம் எளிதான பராமரிப்பு மற்றும் மாற்றத்திற்காக ஒருங்கிணைந்த திரையை ஏற்றுக்கொள்கிறது.அதன் அமைப்பு எளிமையானது மற்றும் அசிங்கமானது.உர உற்பத்தியில் வசதியான மற்றும் நிலையான செயல்பாடு ஒரு தவிர்க்க முடியாத கருவியாகும்.
6. மின்னணு அளவு பேக்கேஜிங் இயந்திரம்:
துகள்கள் திரையிடப்பட்ட பிறகு, அவை பேக்கேஜிங் இயந்திரத்தால் தொகுக்கப்படுகின்றன.பேக்கேஜிங் இயந்திரம் அதிக அளவு ஆட்டோமேஷன், எடை, தையல், பேக்கேஜிங் மற்றும் போக்குவரத்து ஆகியவற்றை ஒருங்கிணைக்கிறது, இது விரைவான அளவு பேக்கேஜிங்கை உணர்ந்து பேக்கேஜிங் செயல்முறையை மிகவும் திறமையாகவும் துல்லியமாகவும் செய்கிறது.
7. பெல்ட் கன்வேயர்:
உற்பத்தி செயல்பாட்டில் கன்வேயர் ஒரு தவிர்க்க முடியாத பாத்திரத்தை வகிக்கிறது, ஏனெனில் இது முழு உற்பத்தி வரிசையின் வெவ்வேறு பகுதிகளை இணைக்கிறது.இந்த கலவை உர உற்பத்தி வரிசையில், உங்களுக்கு பெல்ட் கன்வேயரை வழங்க நாங்கள் தேர்வு செய்கிறோம்.மற்ற வகை கன்வேயர்களுடன் ஒப்பிடும்போது, பெல்ட் கன்வேயர்கள் பெரிய கவரேஜ் கொண்டவை, உங்கள் உற்பத்தி செயல்முறையை மிகவும் திறமையாகவும் சிக்கனமாகவும் ஆக்குகிறது.