இரசாயன உரம் என்றும் அழைக்கப்படும் கூட்டு உரம், இரசாயன எதிர்வினைகள் அல்லது கலவை முறைகள் மூலம் ஒருங்கிணைக்கப்பட்ட நைட்ரஜன், பாஸ்பரஸ் மற்றும் பொட்டாசியம் போன்ற பயிர் ஊட்டச்சத்துக்களின் இரண்டு அல்லது மூன்று ஊட்டச்சத்துக்களைக் கொண்ட உரமாகும்;கலவை உரங்கள் தூள் அல்லது சிறுமணியாக இருக்கலாம்.கலப்பு உரத்தில் அதிக செயலில் உள்ள பொருட்கள் உள்ளன, தண்ணீரில் எளிதில் கரையக்கூடியது, விரைவாக சிதைந்து, வேர்களால் உறிஞ்சப்படுவது எளிது.எனவே, இது "விரைவாக செயல்படும் உரம்" என்று அழைக்கப்படுகிறது.அதன் செயல்பாடு பல்வேறு உற்பத்தி நிலைகளில் பல்வேறு ஊட்டச்சத்துக்களின் விரிவான தேவை மற்றும் சமநிலையை பூர்த்தி செய்வதாகும்.
50,000 டன் கூட்டு உரங்களின் வருடாந்திர உற்பத்தி வரிசையானது மேம்பட்ட உபகரணங்களின் கலவையாகும்.உற்பத்தி செலவுகள் திறமையற்றவை.பல்வேறு கலப்பு மூலப்பொருட்களின் கிரானுலேஷனுக்கு கலவை உர உற்பத்தி வரியைப் பயன்படுத்தலாம்.இறுதியாக, வெவ்வேறு செறிவுகள் மற்றும் சூத்திரங்கள் கொண்ட கலவை உரங்களை உண்மையான தேவைகளுக்கு ஏற்ப தயார் செய்து, பயிர்களுக்குத் தேவையான ஊட்டச்சத்துக்களை திறம்பட நிரப்பி, பயிர் தேவைக்கும் மண் வழங்கலுக்கும் இடையே உள்ள முரண்பாட்டைத் தீர்க்கலாம்.
பொட்டாசியம் நைட்ரஜன், பாஸ்பரஸ் பொட்டாசியம் பெர்பாஸ்பேட், பொட்டாசியம் குளோரைடு, சிறுமணி சல்பேட், சல்பூரிக் அமிலம், அம்மோனியம் நைட்ரேட் மற்றும் பிற வெவ்வேறு சூத்திரங்கள் போன்ற பல்வேறு சூத்திரங்களின் கலவை உரங்களை தயாரிக்க கலப்பு உர உற்பத்தி வரி முக்கியமாகப் பயன்படுத்தப்படுகிறது.
உர உற்பத்தி வரிசை உபகரணங்களின் தொழில்முறை உற்பத்தியாளராக, நாங்கள் வாடிக்கையாளர்களுக்கு உற்பத்தி உபகரணங்களை வழங்குகிறோம் மற்றும் வருடத்திற்கு 10,000 டன்கள் முதல் வருடத்திற்கு 200,000 டன்கள் வரை வெவ்வேறு உற்பத்தி திறன் தேவைகளுக்கு மிகவும் பொருத்தமான தீர்வை வழங்குகிறோம்.நிலையான செயல்பாடு, நல்ல ஆற்றல்-சேமிப்பு விளைவு, குறைந்த பராமரிப்பு செலவு மற்றும் வசதியான செயல்பாடு ஆகியவற்றைக் கொண்ட முழுமையான சாதனங்கள் கச்சிதமான, நியாயமான மற்றும் அறிவியல் பூர்வமானவை.கலவை உரம் (கலப்பு உரம்) உற்பத்தியாளர்களுக்கு இது மிகவும் சிறந்த தேர்வாகும்.
கலப்பு உர உற்பத்தி வரிசையானது பல்வேறு பயிர்களிலிருந்து அதிக, நடுத்தர மற்றும் குறைந்த செறிவு கொண்ட கலவை உரங்களை உற்பத்தி செய்ய முடியும்.பொதுவாக, கலவை உரத்தில் குறைந்தது இரண்டு அல்லது மூன்று ஊட்டச்சத்துக்கள் (நைட்ரஜன், பாஸ்பரஸ், பொட்டாசியம்) உள்ளன.இது அதிக ஊட்டச்சத்து உள்ளடக்கம் மற்றும் சில பக்க விளைவுகளைக் கொண்டுள்ளது.சமச்சீர் உரமிடுவதில் கூட்டு உரம் முக்கிய பங்கு வகிக்கிறது.இது உரமிடுதல் திறனை மேம்படுத்துவது மட்டுமல்லாமல், பயிர்களின் நிலையான மற்றும் அதிக மகசூலை ஊக்குவிக்கும்.
கலவை உர உற்பத்தி வரியின் பயன்பாடு:
1. சல்பர்-பேஜ் யூரியாவின் உற்பத்தி செயல்முறை.
2. கரிம மற்றும் கனிம கலவை உரங்களின் வெவ்வேறு உற்பத்தி செயல்முறைகள்.
3. அமில உர செயல்முறை.
4. தூள் தொழில்துறை கனிம உர செயல்முறை.
5. பெரிய தானிய யூரியா உற்பத்தி செயல்முறை.
6. நாற்றுகளுக்கு மேட்ரிக்ஸ் உரம் உற்பத்தி செயல்முறை.
கரிம உர உற்பத்திக்கு கிடைக்கும் மூலப்பொருட்கள்:
கலவை உர உற்பத்தி வரிசையின் மூலப்பொருட்கள் யூரியா, அம்மோனியம் குளோரைடு, அம்மோனியம் சல்பேட், திரவ அம்மோனியா, அம்மோனியம் பாஸ்பேட், டைஅமோனியம் பாஸ்பேட், பொட்டாசியம் குளோரைடு, பொட்டாசியம் சல்பேட், சில களிமண் மற்றும் பிற கலப்படங்கள் உட்பட.
1) நைட்ரஜன் உரங்கள்: அம்மோனியம் குளோரைடு, அம்மோனியம் சல்பேட், அம்மோனியம் தியோ, யூரியா, கால்சியம் நைட்ரேட் போன்றவை.
2) பொட்டாசியம் உரங்கள்: பொட்டாசியம் சல்பேட், புல் மற்றும் சாம்பல் போன்றவை.
3) பாஸ்பரஸ் உரங்கள்: கால்சியம் பெர்பாஸ்பேட், கனமான கால்சியம் பெர்பாஸ்பேட், கால்சியம் மெக்னீசியம் மற்றும் பாஸ்பேட் உரம், பாஸ்பேட் தாது தூள் போன்றவை.
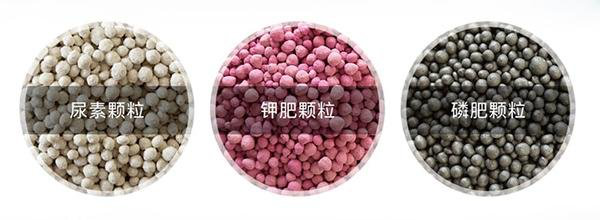
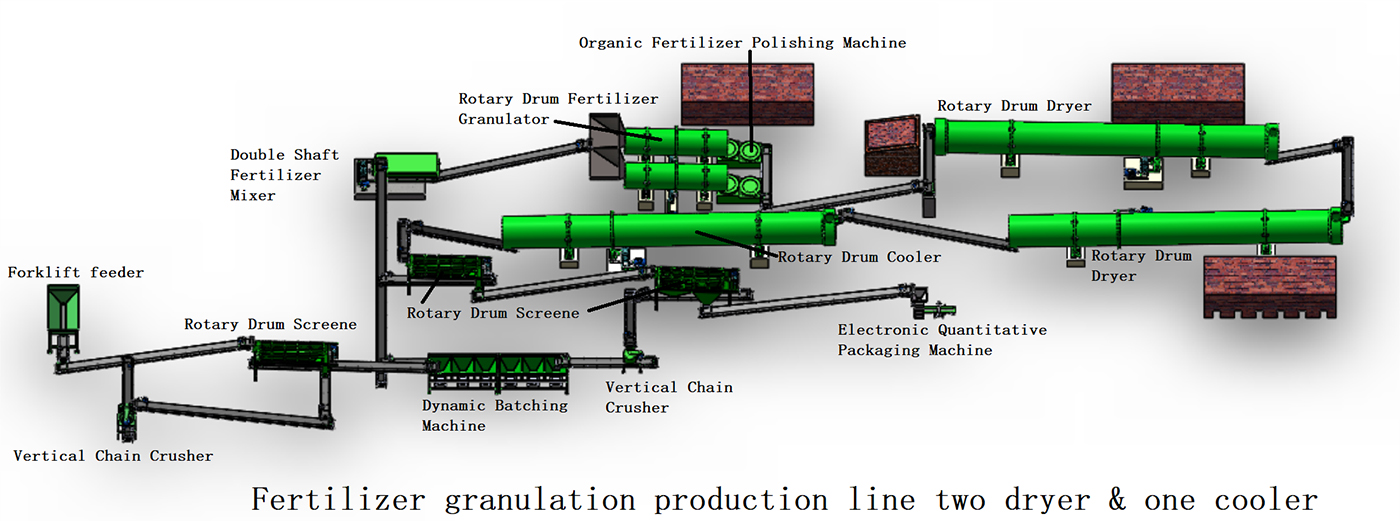
கலப்பு உர உற்பத்தி வரி ரோட்டரி டிரம் கிரானுலேஷன் முக்கியமாக அதிக செறிவு கலவை உரங்களை உற்பத்தி செய்ய பயன்படுத்தப்படுகிறது.கலவை உர எதிர்ப்பு தொழில்நுட்பம், உயர் நைட்ரஜன் கலவை உர உற்பத்தி தொழில்நுட்பம் போன்றவற்றுடன் இணைந்து அதிக மற்றும் குறைந்த செறிவு கொண்ட கலவை உர தொழில்நுட்பத்தை உருவாக்க வட்ட வட்டு கிரானுலேஷன் பயன்படுத்தப்படலாம்.
எங்கள் தொழிற்சாலையின் கலவை உர உற்பத்தி வரிசை பின்வரும் பண்புகளைக் கொண்டுள்ளது:
மூலப்பொருட்கள் பரவலாகப் பயன்படுத்தப்படுகின்றன: கலவை உரங்கள் வெவ்வேறு சூத்திரங்கள் மற்றும் கலவை உரங்களின் விகிதங்களின்படி தயாரிக்கப்படலாம், மேலும் கரிம மற்றும் கனிம கலவை உரங்களின் உற்பத்திக்கு ஏற்றது.
குறைந்தபட்ச கோள விகிதம் மற்றும் பயோபாக்டீரியம் விளைச்சல் அதிகமாக உள்ளது: புதிய செயல்முறை 90% முதல் 95% வரை கோள விகிதத்தை அடைய முடியும், மேலும் குறைந்த வெப்பநிலை காற்று உலர்த்தும் தொழில்நுட்பம் நுண்ணுயிர் பாக்டீரியாவை 90% க்கும் அதிகமான உயிர்வாழும் விகிதத்தை அடையச் செய்யலாம்.முடிக்கப்பட்ட தயாரிப்பு தோற்றத்திலும், அளவிலும் அழகாக இருக்கிறது, இதில் 90% துகள்கள் 2 முதல் 4 மிமீ அளவு கொண்ட துகள்கள்.
தொழிலாளர் செயல்முறை நெகிழ்வானது: கலவை உர உற்பத்தி வரியின் செயல்முறை உண்மையான மூலப்பொருட்கள், சூத்திரம் மற்றும் தளத்தின் படி சரிசெய்யப்படலாம் அல்லது வாடிக்கையாளர்களின் உண்மையான தேவைகளுக்கு ஏற்ப தனிப்பயனாக்கப்பட்ட செயல்முறையை வடிவமைக்க முடியும்.
முடிக்கப்பட்ட பொருட்களின் ஊட்டச்சத்துக்களின் விகிதம் நிலையானது: மூலப்பொருட்களின் தானியங்கு அளவீடு, பல்வேறு திடப்பொருட்களின் துல்லியமான அளவீடு, திரவங்கள் மற்றும் பிற மூலப்பொருட்களின் மூலம், செயல்முறை முழுவதும் ஒவ்வொரு ஊட்டச்சத்தின் நிலைத்தன்மையையும் செயல்திறனையும் கிட்டத்தட்ட பராமரித்தல்.
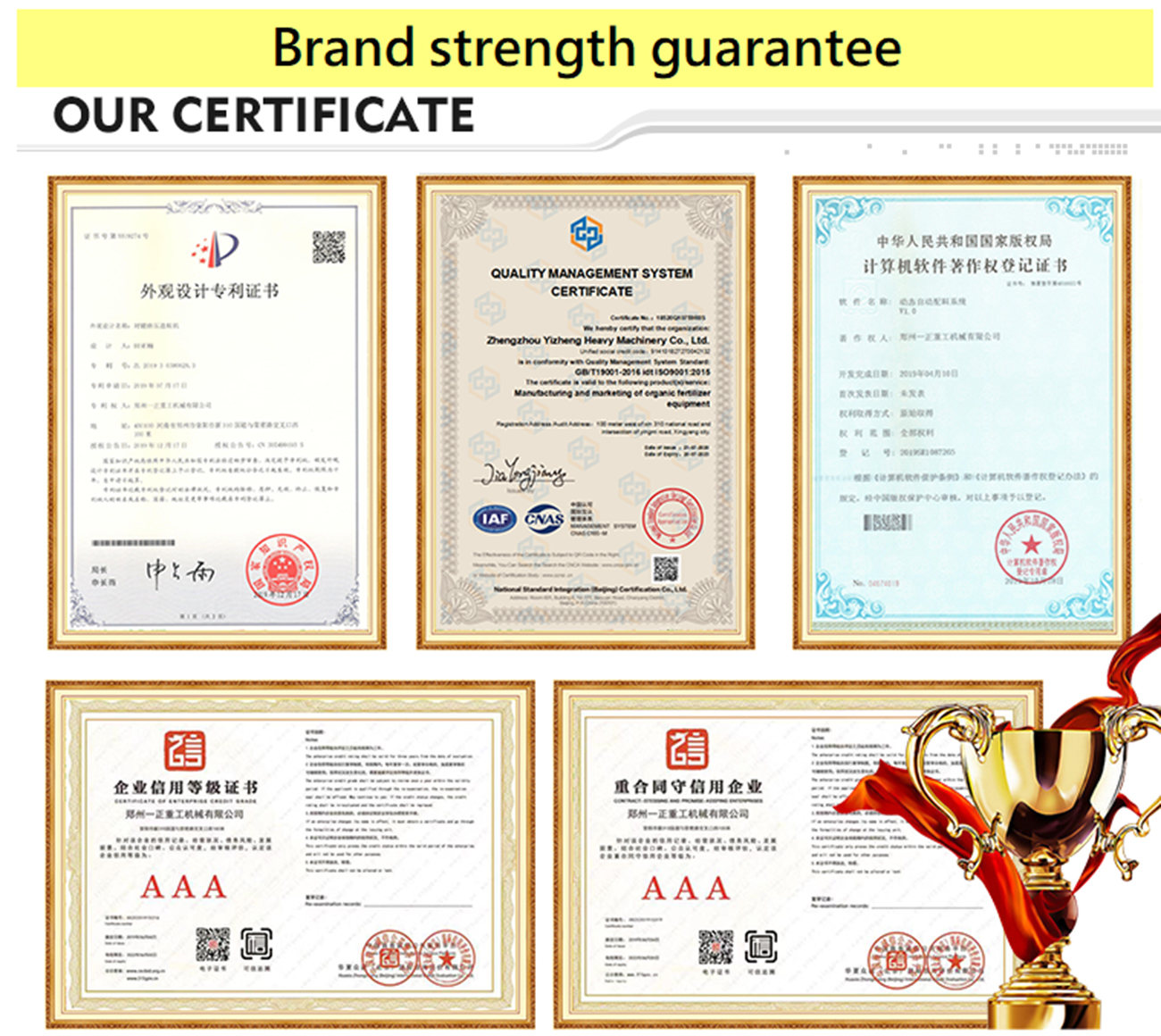
கலப்பு உர உற்பத்தி வரிசையின் செயல்முறை ஓட்டத்தை பொதுவாக பிரிக்கலாம்: மூலப்பொருட்கள், கலவை, முடிச்சுகளை நசுக்குதல், கிரானுலேஷன், ஆரம்ப திரையிடல், துகள் உலர்த்துதல், துகள் குளிரூட்டல், இரண்டாம் நிலை திரையிடல், முடிக்கப்பட்ட துகள் பூச்சு மற்றும் முடிக்கப்பட்ட பொருட்களின் அளவு பேக்கேஜிங்.
1. மூலப்பொருள் பொருட்கள்:
சந்தை தேவை மற்றும் உள்ளூர் மண் நிர்ணய முடிவுகளின்படி, யூரியா, அம்மோனியம் நைட்ரேட், அம்மோனியம் குளோரைடு, அம்மோனியம் தியோபாஸ்பேட், அம்மோனியம் பாஸ்பேட், டைஅமோனியம் பாஸ்பேட், கனமான கால்சியம், பொட்டாசியம் குளோரைடு (பொட்டாசியம் சல்பேட்) மற்றும் பிற மூலப்பொருட்கள் ஒரு குறிப்பிட்ட விகிதத்தில் விநியோகிக்கப்படுகின்றன.சேர்க்கைகள், சுவடு கூறுகள் போன்றவை பெல்ட் செதில்கள் மூலம் ஒரு குறிப்பிட்ட விகிதத்தில் பொருட்களாகப் பயன்படுத்தப்படுகின்றன.ஃபார்முலா விகிதத்தின்படி, அனைத்து மூலப்பொருள் பொருட்களும் பெல்ட்களிலிருந்து மிக்சர்களுக்கு சமமாக பாய்கின்றன, இது ப்ரீமிக்ஸ் என்று அழைக்கப்படுகிறது.இது உருவாக்கத்தின் துல்லியத்தை உறுதி செய்கிறது மற்றும் திறமையான தொடர்ச்சியான பொருட்களை அடைகிறது.
2. கலவை:
தயாரிக்கப்பட்ட மூலப்பொருட்கள் முழுமையாக கலக்கப்பட்டு சமமாக கிளறி, உயர் செயல்திறன் மற்றும் உயர்தர சிறுமணி உரத்திற்கான அடித்தளத்தை அமைக்கிறது.ஒரு கிடைமட்ட கலவை அல்லது வட்டு கலவையை சீரான கலவை மற்றும் கிளறலுக்கு பயன்படுத்தலாம்.
3. நொறுக்கு:
பொருளில் உள்ள கட்டிகள் சமமாக கலந்த பிறகு நசுக்கப்படுகின்றன, இது அடுத்தடுத்த கிரானுலேஷன் செயலாக்கத்திற்கு வசதியானது, முக்கியமாக செயின் க்ரஷரைப் பயன்படுத்துகிறது.
4. கிரானுலேஷன்:
சமமாக கலந்து நசுக்கப்பட்ட பிறகு, பெல்ட் கன்வேயர் மூலம் கிரானுலேஷன் இயந்திரத்திற்கு பொருள் கொண்டு செல்லப்படுகிறது, இது கலப்பு உர உற்பத்தி வரிசையின் முக்கிய பகுதியாகும்.கிரானுலேட்டரின் தேர்வு மிகவும் முக்கியமானது.எங்கள் தொழிற்சாலை டிஸ்க் கிரானுலேட்டர், டிரம் கிரானுலேட்டர், ரோலர் எக்ஸ்ட்ரூடர் அல்லது கலவை உர கிரானுலேட்டர் ஆகியவற்றை உற்பத்தி செய்கிறது.
5. திரையிடல்:
துகள்கள் sieved, மற்றும் தகுதியற்ற துகள்கள் மீண்டும் செயலாக்க மேல் கலவை மற்றும் கிளறி இணைப்பு திரும்ப.பொதுவாக, ஒரு ரோலர் சல்லடை இயந்திரம் பயன்படுத்தப்படுகிறது.
6. பேக்கேஜிங்:
இந்த செயல்முறை ஒரு தானியங்கி அளவு பேக்கேஜிங் இயந்திரத்தை ஏற்றுக்கொள்கிறது.இயந்திரம் ஒரு தானியங்கி எடையிடும் இயந்திரம், ஒரு கன்வேயர் அமைப்பு, ஒரு சீல் இயந்திரம் போன்றவற்றைக் கொண்டுள்ளது. வாடிக்கையாளர் தேவைகளுக்கு ஏற்ப நீங்கள் ஹாப்பர்களை உள்ளமைக்கலாம்.இது கரிம உரம் மற்றும் கலவை உரம் போன்ற மொத்தப் பொருட்களின் அளவு பேக்கேஜிங்கை உணர முடியும், மேலும் உணவு பதப்படுத்தும் தொழிற்சாலைகள் மற்றும் தொழில்துறை உற்பத்தி வரிகளில் பரவலாகப் பயன்படுத்தப்படுகிறது.