கலவை உர உற்பத்தி வரிசையில் எங்களுக்கு முழுமையான அனுபவம் உள்ளது.உற்பத்திச் செயல்பாட்டில் உள்ள ஒவ்வொரு செயல்முறை இணைப்பின் மீதும் நாங்கள் கவனம் செலுத்துவது மட்டுமல்லாமல், ஒவ்வொரு முழு உற்பத்தி வரிசையின் செயல்முறை விவரங்களையும் எப்பொழுதும் புரிந்துகொண்டு, சுமூகமாக ஒன்றோடொன்று இணைக்கிறோம்.வாடிக்கையாளர்களின் உண்மையான தேவைகளுக்கு ஏற்ப தனிப்பயனாக்கப்பட்ட உற்பத்தி வரி தீர்வுகளை நாங்கள் வழங்குகிறோம்.
யுஜெங் ஹெவி இண்டஸ்ட்ரீஸ் உடனான உங்கள் ஒத்துழைப்பின் முக்கிய நன்மைகளில் முழுமையான உற்பத்தி செயல்முறை ஒன்றாகும்.டிரம் கிரானுலேஷன் உற்பத்தி வரிகளின் முழுமையான தொகுப்பின் செயல்முறை வடிவமைப்பு மற்றும் உற்பத்தியை நாங்கள் வழங்குகிறோம்.
சிக்கலான உரம் என்பது நைட்ரஜன், பாஸ்பரஸ் மற்றும் பொட்டாசியம் ஆகியவற்றைக் கொண்ட ஒரு கலவை உரமாகும், இது ஒரு குறிப்பிட்ட உரத்தின் குறிப்பிட்ட விகிதத்தின் படி கலக்கப்படுகிறது மற்றும் இரசாயன எதிர்வினைகளால் ஒருங்கிணைக்கப்படுகிறது.ஊட்டச்சத்து உள்ளடக்கம் சீரானது மற்றும் துகள் அளவு ஒரே மாதிரியாக இருக்கும்.கலவை உர உற்பத்தி வரிசையானது பல்வேறு கலவை உர மூலப்பொருட்களின் கிரானுலேஷனுக்கு பரந்த தழுவல் தன்மையைக் கொண்டுள்ளது.
கலவை உரமானது சீரான கிரானுலேஷன், பளபளப்பான நிறம், நிலையான தரம் மற்றும் பயிர்களால் உறிஞ்சப்படுவதற்கு எளிதாகக் கரைதல் போன்ற பண்புகளைக் கொண்டுள்ளது.குறிப்பாக, விதைகள் உரங்களை வளர்ப்பது ஒப்பீட்டளவில் பாதுகாப்பானது.அனைத்து வகையான மண் மற்றும் கோதுமை, சோளம், முலாம்பழம் மற்றும் பழங்கள், வேர்க்கடலை, காய்கறிகள், பீன்ஸ், பூக்கள், பழ மரங்கள் மற்றும் பிற பயிர்களுக்கு ஏற்றது.இது அடிப்படை உரம், உரம், உரம் துரத்தல், உரம் மற்றும் நீர்ப்பாசனத்திற்கு ஏற்றது.
கலவை உர உற்பத்திக்கான மூலப்பொருட்களில் யூரியா, அம்மோனியம் குளோரைடு, அம்மோனியம் சல்பேட், திரவ அம்மோனியா, அம்மோனியம் மோனோபாஸ்பேட், டைஅமோனியம் பாஸ்பேட், பொட்டாசியம் குளோரைடு, பொட்டாசியம் சல்பேட், சில களிமண் மற்றும் பிற கலப்படங்கள் அடங்கும்.மண்ணின் தேவைகளுக்கு ஏற்ப பல்வேறு கரிம பொருட்கள் சேர்க்கப்படுகின்றன:
1. விலங்குகளின் கழிவுகள்: கோழி, பன்றியின் சாணம், ஆட்டுச் சாணம், கால்நடைப் பாடுதல், குதிரை எரு, முயல் எரு போன்றவை.
2, தொழிற்சாலை கழிவுகள்: திராட்சை, வினிகர் கசடு, மரவள்ளிக் கிழங்கு எச்சம், சர்க்கரை எச்சம், உயிர்வாயு கழிவு, ஃபர் எச்சம் போன்றவை.
3. விவசாய கழிவுகள்: பயிர் வைக்கோல், சோயாபீன் மாவு, பருத்தி விதை தூள் போன்றவை.
4. வீட்டுக் கழிவுகள்: சமையலறைக் குப்பை
5, கசடு: நகர்ப்புறக் கசடு, நதிக் கசடு, வடிகட்டிக் கசடு போன்றவை.
கலவை உர உற்பத்தி வரிசையில் ஒரு மாறும் மூலப்பொருள், இரண்டு-அச்சு கலப்பான், ஒரு புதிய கலவை உர கிரானுலேட்டர், ஒரு செங்குத்து சங்கிலி நொறுக்கி, ஒரு டிரம் உலர்த்தும் குளிர்விப்பான், ஒரு டிரம் சல்லடை இயந்திரம், ஒரு பூச்சு இயந்திரம், ஒரு தூசி சேகரிப்பான், ஒரு தானியங்கி பேக்கேஜிங் ஆகியவை பொருத்தப்பட்டுள்ளன. இயந்திரம் மற்றும் பிற துணை உபகரணங்கள்.
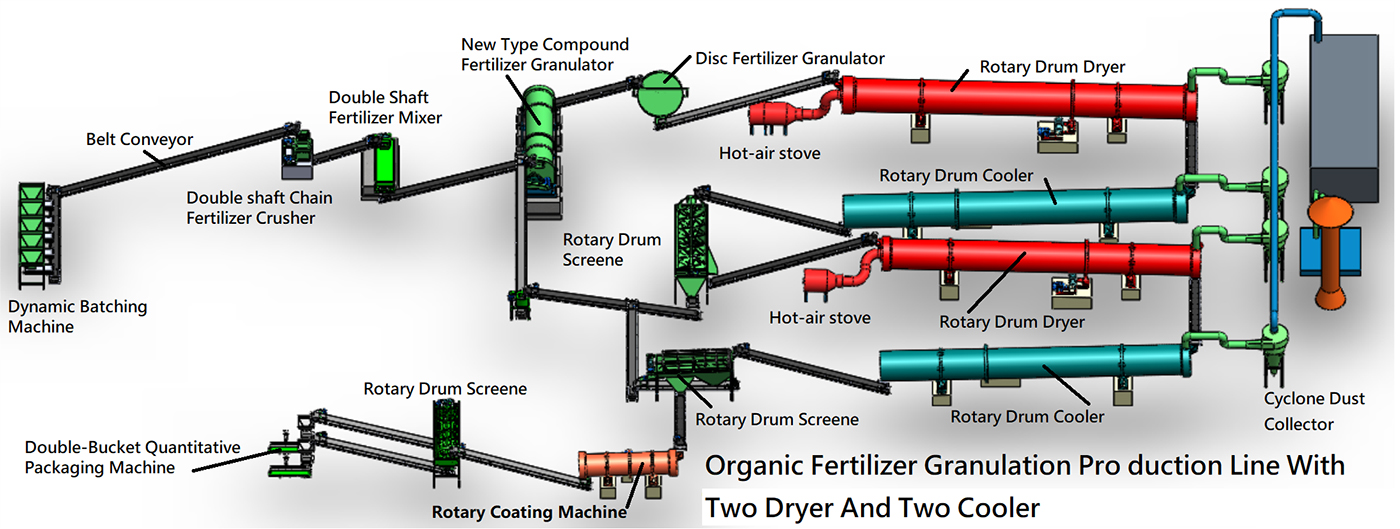
உர உற்பத்தி வரிசை உபகரணங்களின் தொழில்முறை உற்பத்தியாளராக, நாங்கள் வாடிக்கையாளர்களுக்கு ஆண்டுக்கு 10,000 டன்கள் முதல் வருடத்திற்கு 200,000 டன்கள் வரை உற்பத்தி வரிகளை வழங்குகிறோம்.
1. மேம்பட்ட டிரம் கிரானுலேஷன் இயந்திரத்துடன் கிரானுலேஷன் விகிதம் 70% வரை அதிகமாக உள்ளது.
2. முக்கிய கூறுகள் உடைகள்-எதிர்ப்பு மற்றும் அரிப்பு-எதிர்ப்பு பொருட்களை ஏற்றுக்கொள்கின்றன, மேலும் உபகரணங்கள் நீண்ட சேவை வாழ்க்கை உள்ளது.
3. ரோட்டரி டிரம் கிரானுலேட்டர் சிலிகான் அல்லது துருப்பிடிக்காத எஃகு தகடுகளுடன் வரிசையாக உள்ளது, மேலும் இயந்திரத்தின் உள் சுவரில் பொருள் ஒட்டுவது எளிதானது அல்ல.
4. நிலையான செயல்பாடு, வசதியான பராமரிப்பு, அதிக செயல்திறன் மற்றும் குறைந்த ஆற்றல் நுகர்வு.
5. தொடர்ச்சியான உற்பத்தியை அடைய முழு உற்பத்தி வரிசையையும் இணைக்க பெல்ட் கன்வேயரைப் பயன்படுத்தவும்.
6. சுற்றுச்சூழல் பாதுகாப்பிற்காக வால் வாயுவை சுத்திகரிக்க இரண்டு செட் தூசி அகற்றும் அறைகளைப் பயன்படுத்தவும்.
7. இரண்டு சல்லடைகளின் உழைப்பைப் பிரிப்பது, துகள் அளவு சீரானதாகவும், தரம் தகுதியானதாகவும் இருப்பதை உறுதி செய்கிறது.
8. சீரான கலவை, உலர்த்துதல், குளிர்வித்தல், பூச்சு மற்றும் பிற செயல்முறைகள் முடிக்கப்பட்ட தயாரிப்பை தரத்தில் சிறந்ததாக ஆக்குகின்றன.
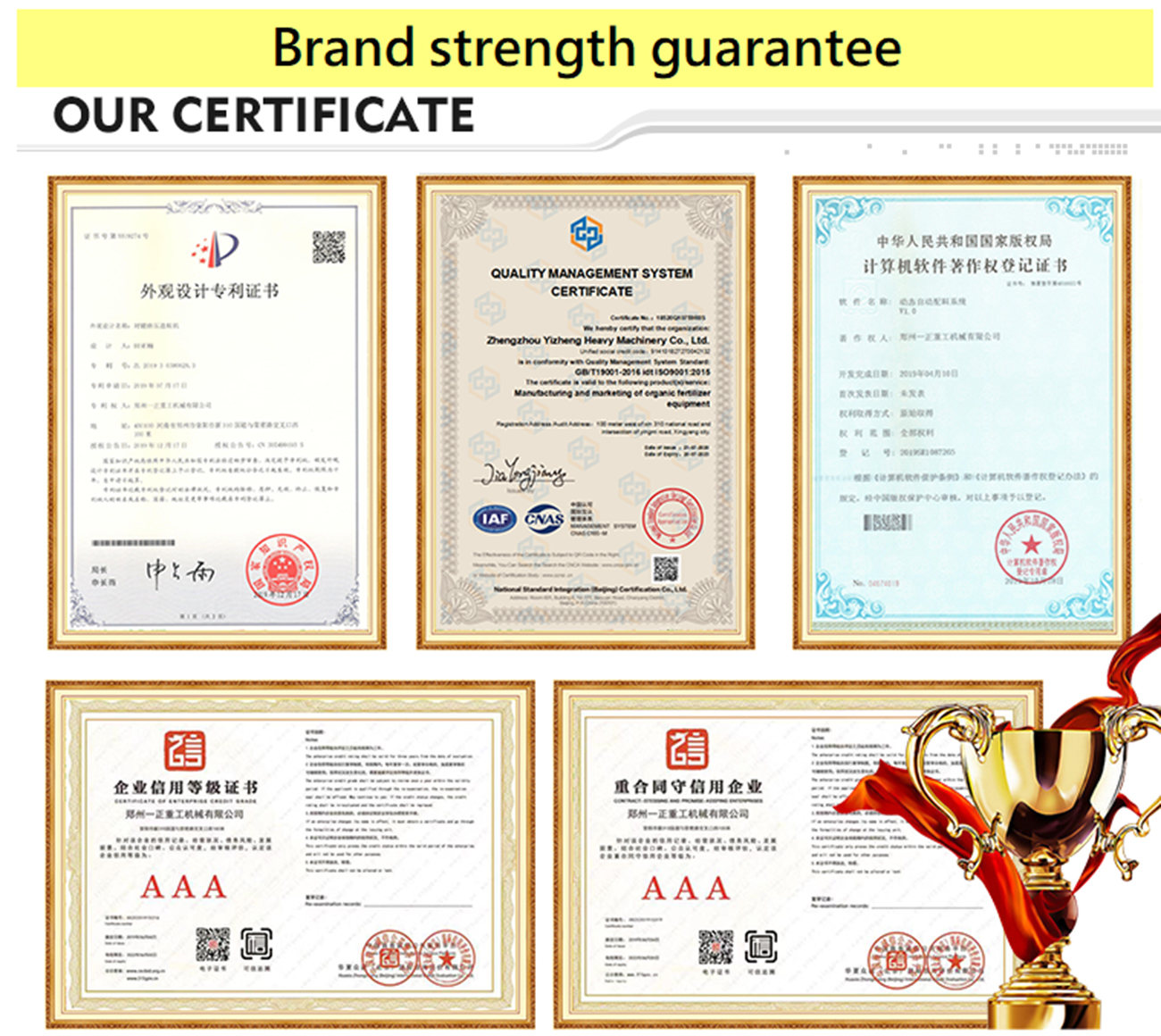
கலவை உர உற்பத்தி வரியின் செயல்முறை ஓட்டம்: மூலப்பொருட்கள் → மூலப்பொருள் கலவை → கிரானுலேஷன் → உலர்த்துதல் → குளிர்வித்தல் → முடிக்கப்பட்ட தயாரிப்பு திரையிடல் → பிளாஸ்டிக் துகள் துண்டு துண்டாக → பூச்சு → முடிக்கப்பட்ட தயாரிப்பு பேக்கேஜிங் → சேமிப்பு.குறிப்பு: இந்த தயாரிப்பு வரி குறிப்புக்கு மட்டுமே.
மூலப்பொருட்கள்:
சந்தை தேவை மற்றும் உள்ளூர் மண் நிர்ணய முடிவுகளின்படி, யூரியா, அம்மோனியம் நைட்ரேட், அம்மோனியம் குளோரைடு, அம்மோனியம் தியோபாஸ்பேட், அம்மோனியம் பாஸ்பேட், டைஅமோனியம் பாஸ்பேட், கனமான கால்சியம், பொட்டாசியம் குளோரைடு (பொட்டாசியம் சல்பேட்) மற்றும் பிற மூலப்பொருட்கள் ஒரு குறிப்பிட்ட விகிதத்தில் விநியோகிக்கப்படுகின்றன.சேர்க்கைகள், சுவடு கூறுகள் போன்றவை பெல்ட் செதில்கள் மூலம் ஒரு குறிப்பிட்ட விகிதத்தில் பொருட்களாகப் பயன்படுத்தப்படுகின்றன.ஃபார்முலா விகிதத்தின்படி, அனைத்து மூலப்பொருள் பொருட்களும் பெல்ட்களிலிருந்து மிக்சர்களுக்கு சமமாக பாய்கின்றன, இது ப்ரீமிக்ஸ் என்று அழைக்கப்படுகிறது.இது உருவாக்கத்தின் துல்லியத்தை உறுதி செய்கிறது மற்றும் திறமையான தொடர்ச்சியான பொருட்களை அடைகிறது.
1. கலவை:
தயாரிக்கப்பட்ட மூலப்பொருட்கள் முழுமையாக கலக்கப்பட்டு சமமாக கிளறி, உயர் செயல்திறன் மற்றும் உயர்தர சிறுமணி உரத்திற்கான அடித்தளத்தை அமைக்கிறது.ஒரு கிடைமட்ட கலவை அல்லது வட்டு கலவையை சீரான கலவை மற்றும் கிளறலுக்கு பயன்படுத்தலாம்.
2. கிரானுலேஷன்:
சமமாக கலந்து நசுக்கிய பிறகு பொருள் பெல்ட் கன்வேயரில் இருந்து புதிய கலவை உர கிரானுலேட்டருக்கு கொண்டு செல்லப்படுகிறது.டிரம்மின் தொடர்ச்சியான சுழற்சியுடன், பொருள் ஒரு குறிப்பிட்ட பாதையில் உருளும் இயக்கத்தை உருவாக்குகிறது.உருவாக்கப்படும் வெளியேற்ற அழுத்தத்தின் கீழ், பொருள் மீண்டும் சிறிய துகள்களாக இணைக்கப்பட்டு, சுற்றியுள்ள தூளுடன் இணைக்கப்பட்டு படிப்படியாக தகுதியான கோள வடிவத்தை உருவாக்குகிறது.துகள்கள்.
3. உலர் துகள்கள்:
துகள் ஈரப்பதத்தின் தேவைகளைப் பூர்த்தி செய்வதற்கு முன் கிரானுலேஷன் பொருள் உலர்த்தப்பட வேண்டும்.உலர்த்தி சுழலும் போது, உள் தூக்கும் தகடு தொடர்ந்து மோல்டிங் துகள்களை தூக்கி எறிகிறது, இதனால் பொருள் வெப்பமான காற்றுடன் முழுமையாக தொடர்பு கொண்டு ஈரப்பதத்தை எடுத்துச் செல்கிறது, இதனால் சீரான உலர்த்தும் இலக்கை அடைய முடியும்.வெளியேற்ற வாயுக்களை மையமாக வெளியேற்றவும் ஆற்றலைச் சேமிக்கவும் நுகர்வு குறைக்கவும் இது ஒரு சுயாதீனமான காற்று சுத்திகரிப்பு முறையைப் பின்பற்றுகிறது.
4. கிரானுல் கூலிங்:
பொருள் துகள்கள் காய்ந்த பிறகு, அவை குளிரூட்டலுக்கு குளிரூட்டிக்கு அனுப்பப்பட வேண்டும்.குளிரூட்டியானது பெல்ட் கன்வேயர் மூலம் உலர்த்தியுடன் இணைக்கப்பட்டுள்ளது.குளிரூட்டல் தூசியை அகற்றலாம், குளிரூட்டும் திறன் மற்றும் வெப்ப ஆற்றல் பயன்பாட்டை மேம்படுத்தலாம் மற்றும் துகள்களில் இருந்து ஈரப்பதத்தை மேலும் அகற்றலாம்.
5. திரையிடல்:
பொருள் துகள்கள் குளிர்ந்த பிறகு, அனைத்து பெரிய மற்றும் பெரிய துகள்கள் ஒரு ரோலர் சல்லடை மூலம் திரையிடப்படுகின்றன.பெல்ட் கன்வேயரில் இருந்து பிளெண்டருக்கு சல்லடை செய்யப்பட்ட தகுதியற்ற பொருட்கள் மீண்டும் மூலப்பொருட்களுடன் கலக்கப்பட்டு கிரானுலேட் செய்யப்படுகின்றன.முடிக்கப்பட்ட தயாரிப்பு கலவை உர பூச்சு இயந்திரத்திற்கு கொண்டு செல்லப்படும்.
6. மெனிங்:
துகள்களின் அடுக்கு ஆயுளை திறம்பட மேம்படுத்தவும், துகள்களை மென்மையாக்கவும், அரை முடிக்கப்பட்ட துகள்களின் மேற்பரப்பில் ஒரு சீரான பாதுகாப்புத் திரைப்படத்தைப் பயன்படுத்துவதற்கு இது முக்கியமாகப் பயன்படுத்தப்படுகிறது.பூச்சுக்குப் பிறகு, முழு உற்பத்தி செயல்முறையிலும் இது கடைசி இணைப்பு - பேக்கேஜிங்.
7. பேக்கேஜிங்:
இந்த செயல்முறை ஒரு தானியங்கி அளவு பேக்கேஜிங் இயந்திரத்தை ஏற்றுக்கொள்கிறது.இயந்திரம் ஒரு தானியங்கி எடையிடும் இயந்திரம், ஒரு கன்வேயர் அமைப்பு, ஒரு சீல் இயந்திரம் போன்றவற்றைக் கொண்டுள்ளது. வாடிக்கையாளர் தேவைகளுக்கு ஏற்ப நீங்கள் ஹாப்பர்களை உள்ளமைக்கலாம்.கரிம உரம் மற்றும் கூட்டு உரம் போன்ற மொத்தப் பொருட்களின் அளவு பேக்கேஜிங்கை இது உணர முடியும்.