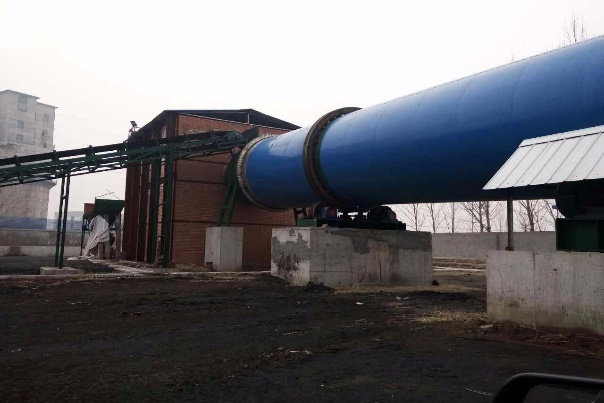
Iகலப்பு உர உற்பத்தி வரி அறிமுகம்
கூட்டு உரம் என்பது N, P இன் இரண்டு அல்லது மூன்று சத்துக்களைக் கொண்ட உரமாகும்;K. கலவை உரம் தூள் அல்லது சிறுமணி வடிவில் கிடைக்கிறது.இது பொதுவாக மேல் உரமாகப் பயன்படுத்தப்படுகிறது மேலும் அடி உரமாகவும் விதை உரமாகவும் பயன்படுத்தப்படலாம்.கலவை உரத்தில் அதிக பயனுள்ள கூறுகள் உள்ளன, எனவே இது தண்ணீரில் எளிதில் கரையக்கூடியது, விரைவாக சிதைகிறது, மேலும் வேர் அமைப்பால் எளிதில் உறிஞ்சப்படுகிறது, எனவே இது "விரைவாக செயல்படும் உரம்" என்று அழைக்கப்படுகிறது.பல்வேறு நிலைமைகளின் கீழ் பயிர்களுக்குத் தேவையான பல்வேறு ஊட்டச்சத்துக்களை விரிவான தேவையைப் பூர்த்தி செய்து சமநிலைப்படுத்துவதே இதன் செயல்பாடு.
இந்த உர உற்பத்தி வரிசை முக்கியமாக NPK, GSSP, SSP, கிரானுலேட்டட் பொட்டாசியம் சல்பேட், சல்பூரிக் அமிலம், அம்மோனியம் நைட்ரேட் மற்றும் பிற பொருட்களைப் பயன்படுத்தி கலவை உரத் துகள்களை துகள்களாக மாற்றப் பயன்படுகிறது.கலவை உர உபகரணமானது நிலையானது, குறைந்த செயலிழப்பு விகிதம், சிறிய பராமரிப்பு மற்றும் குறைந்த விலை ஆகியவற்றின் நன்மைகளைக் கொண்டுள்ளது.
முழு உற்பத்தி வரிசையும் மேம்பட்ட மற்றும் திறமையான உபகரணங்களுடன் பொருத்தப்பட்டுள்ளது, இது ஆண்டுக்கு 50,000 டன் கலவை உர உற்பத்தியை அடைய முடியும்.உண்மையான உற்பத்தித் திறன் தேவைகளின்படி, 10,000 ~ 300,000 டன்கள் கொண்ட வெவ்வேறு ஆண்டுத் திறன் கொண்ட கலவை உர உற்பத்தி வரிகளை நாங்கள் திட்டமிட்டு வடிவமைக்கிறோம்.உபகரணங்களின் முழு தொகுப்பும் கச்சிதமான, நியாயமான, அறிவியல், நிலையான செயல்பாடு, ஆற்றல் சேமிப்பு, குறைந்த பராமரிப்பு செலவு, செயல்பட எளிதானது, கலவை உர உற்பத்தியாளர்களுக்கு சிறந்த தேர்வாகும்.
நடுத்தர கலவை உர உற்பத்தி வரி செயல்முறை
கலவை உர உற்பத்தி வரிசையின் செயல்முறையை பொதுவாகப் பிரிக்கலாம்: மூலப்பொருள் தொகுப்பு, கலவை, நசுக்குதல், கிரானுலேட்டிங், முதன்மை திரையிடல், சிறுமணி உலர்த்துதல் மற்றும் குளிர்வித்தல், இரண்டாம் நிலை திரையிடல், சிறுமணி பூச்சு மற்றும் அளவு பேக்கேஜிங்.
1. மூலப்பொருட்கள் தொகுப்பு: சந்தை தேவை மற்றும் உள்ளூர் மண் நிர்ணய முடிவுகளின் படி, யூரியா, அம்மோனியம் நைட்ரேட், அம்மோனியம் குளோரைடு, அம்மோனியம் சல்பேட், அம்மோனியம் பாஸ்பேட் (மோனோஅமோனியம் பாஸ்பேட், டைஅமோனியம் பாஸ்பேட், கனமான கால்சியம், பொது கால்சியம்) மற்றும் பொட்டாசியம் குளோரைடு போன்ற மூலப்பொருட்கள் பொட்டாசியம் சல்பேட்) ஒரு குறிப்பிட்ட விகிதத்தில் ஒதுக்கப்பட வேண்டும்.சேர்க்கைகள் மற்றும் சுவடு கூறுகள் பெல்ட் அளவுகோல் மூலம் எடையும் மற்றும் ஒரு குறிப்பிட்ட விகிதத்தில் விகிதாசாரமாகும்.சூத்திர விகிதத்தின் படி, அனைத்து மூலப்பொருட்களும் கலவை மூலம் சமமாக கலக்கப்படுகின்றன.இந்த செயல்முறை ப்ரீமிக்ஸ் என்று அழைக்கப்படுகிறது.இது துல்லியமான உருவாக்கத்தை உறுதி செய்கிறது மற்றும் திறமையான மற்றும் தொடர்ச்சியான தொகுப்பை செயல்படுத்துகிறது.
2. கலவை: தயாரிக்கப்பட்ட மூலப்பொருட்களை முழுமையாக கலந்து, அவற்றை சமமாக கிளறவும், இது திறமையான மற்றும் உயர்தர சிறுமணி உரத்திற்கான அடித்தளத்தை அமைக்கிறது.கிடைமட்ட கலவை அல்லது வட்டு கலவையை சமமாக கலக்க பயன்படுத்தலாம்.
3. நசுக்குதல்: பொருள்களில் உள்ள கேக்கிங்கை நசுக்க, அடுத்தடுத்த கிரானுலேஷன் செயலாக்கத்திற்கு அவசியம்.சங்கிலி நொறுக்கி முக்கியமாக பயன்படுத்தப்படுகிறது.
4. கிரானுலேட்டிங்: சமமாக கிளறப்பட்ட மற்றும் நொறுக்கப்பட்ட பொருட்கள் கிரானுலேட்டருக்கு பெல்ட் கன்வேயர் மூலம் கிரானுலேட்டருக்கு கொண்டு செல்லப்படுகின்றன, இது முழு உற்பத்தி வரிசையின் முக்கிய பகுதியாகும்.கிரானுலேட்டரின் தேர்வு மிகவும் முக்கியமானது, எங்களிடம் டிஸ்க் கிரானுலேட்டர், ரோட்டரி டிரம் கிரானுலேட்டர், ரோலர் எக்ஸ்ட்ரூஷன் கிரானுலேட்டர் அல்லது கலவை உர கிரானுலேட்டர் உள்ளது.
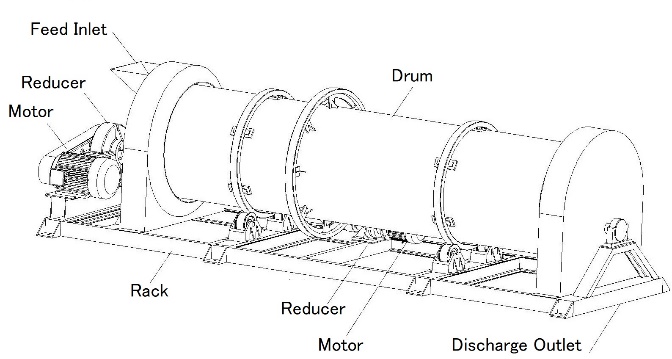
5. முதன்மைத் திரையிடல்: துகள்களுக்கான பூர்வாங்க ஸ்கிரீனிங் எடுத்து, தகுதியற்றவற்றை மறு செயலாக்கத்திற்கு நசுக்குவதற்குத் திருப்பி அனுப்பவும்.பொதுவாக, ரோட்டரி ஸ்கிரீனிங் இயந்திரம் பயன்படுத்தப்படுகிறது.
6. உலர்த்துதல்: முதன்மைத் திரையிடலுக்குப் பிறகு தகுதிவாய்ந்த துகள்கள், முடிக்கப்பட்ட துகள்களின் ஈரப்பதத்தைக் குறைக்க உலர்த்துவதற்காக பெல்ட் கன்வேயர் மூலம் ரோட்டரி உலர்த்திக்குக் கொண்டு செல்லப்படுகிறது.உலர்த்திய பிறகு, துகள்களின் ஈரப்பதம் 20%-30% இலிருந்து 2%-5% வரை குறையும்.
7. துகள்கள் குளிரூட்டல்: உலர்த்திய பிறகு, துகள்கள் குளிரூட்டிக்கு குளிரூட்டிக்கு அனுப்பப்படும், இது பெல்ட் கன்வேயர் மூலம் உலர்த்தியுடன் இணைக்கப்பட்டுள்ளது.குளிரூட்டல் தூசியை நீக்கி, குளிரூட்டும் திறன் மற்றும் வெப்ப பயன்பாட்டு விகிதத்தை மேம்படுத்துகிறது மற்றும் உரத்தில் உள்ள ஈரப்பதத்தை மேலும் நீக்குகிறது.
8. இரண்டாம் நிலை ஸ்கிரீனிங்: குளிர்ந்த பிறகு, அனைத்து தகுதியற்ற துகள்களும் ரோட்டரி ஸ்கிரீனிங் இயந்திரம் மூலம் திரையிடப்பட்டு, பெல்ட் கன்வேயர் மூலம் மிக்சிக்கு கொண்டு செல்லப்பட்டு, பின்னர் மறு செயலாக்கத்திற்கான பிற மூலப்பொருட்களுடன் கலக்கப்படுகிறது.முடிக்கப்பட்ட பொருட்கள் கலவை உர பூச்சு இயந்திரத்திற்கு கொண்டு செல்லப்படும்.
9. பூச்சு: பாதுகாக்கும் காலத்தை திறம்பட நீட்டிக்கவும் மற்றும் துகள்களை மென்மையாக்கவும், அரை-துகள்களின் மேற்பரப்பை ஒரு சீரான பாதுகாப்பு படத்துடன் பூசுவதற்கு இது முக்கியமாகப் பயன்படுத்தப்படுகிறது.பூச்சுக்குப் பிறகு, இங்கே கடைசி செயல்முறைக்கு வாருங்கள் - பேக்கேஜிங்.
10. பேக்கேஜிங் சிஸ்டம்: இந்த செயல்பாட்டில் தானியங்கி அளவு பேக்கேஜிங் இயந்திரம் ஏற்றுக்கொள்ளப்படுகிறது.இயந்திரம் தானியங்கி எடை மற்றும் பேக்கிங் இயந்திரம், கடத்தும் அமைப்பு, சீல் இயந்திரம் மற்றும் பலவற்றைக் கொண்டுள்ளது.வாடிக்கையாளர் தேவைகளுக்கு ஏற்ப ஹாப்பரையும் கட்டமைக்க முடியும்.கரிம உரம் மற்றும் கலவை உரம் போன்ற மொத்தப் பொருட்களின் அளவு பேக்கேஜிங் பல்வேறு தொழில்கள் மற்றும் துறைகளில் பரவலாகப் பயன்படுத்தப்படுகிறது.
கலவை உர உற்பத்தி வரிசையின் தொழில்நுட்பம் மற்றும் அம்சங்கள்:
ரோட்டரி டிரம் கிரானுலேட்டர் முக்கியமாக அதிக செறிவு கொண்ட கலவை உர தொழில்நுட்பத்தின் உற்பத்தியில் பயன்படுத்தப்படுகிறது, டிஸ்க் அல்லாத நீராவி கிரானுலேட்டர் உயர், நடுத்தர மற்றும் குறைந்த செறிவு கொண்ட கலவை உர தொழில்நுட்பத்தின் உற்பத்தியில் பயன்படுத்தப்படலாம், இது எதிர்ப்பு கேக்கிங் தொழில்நுட்பத்துடன் இணைந்து, உயர் நைட்ரஜன் ஆகும். கலவை உர உற்பத்தி தொழில்நுட்பம் மற்றும் பல.எங்கள் கலவை உர உற்பத்தி வரிசையில் பின்வரும் பண்புகள் உள்ளன:
1. மூலப்பொருட்களின் பரவலான பயன்பாடு: கலவை உரங்களை வெவ்வேறு சூத்திரங்கள் மற்றும் விகிதாச்சாரங்களின்படி உற்பத்தி செய்யலாம், மேலும் இது கரிம மற்றும் கனிம கலவை உரங்களின் உற்பத்திக்கும் ஏற்றது.
2. உயர் துகள்கள் உருவாக்கும் விகிதம் மற்றும் உயிரியல் பாக்டீரியா உயிர்வாழும் விகிதம்: புதிய தொழில்நுட்பம் துகள்களை உருவாக்கும் விகிதத்தை 90% ~ 95% ஐ அடையச் செய்யலாம், மேலும் குறைந்த வெப்பநிலை மற்றும் அதிக காற்றில் உலர்த்தும் தொழில்நுட்பம் நுண்ணுயிர் பாக்டீரியாவின் உயிர்வாழ்வு விகிதத்தை உருவாக்கலாம். 90% அடையும்.முடிக்கப்பட்ட தயாரிப்பு தோற்றத்தில் நன்றாகவும், சீரான அளவிலும் உள்ளது, அவற்றில் 90% 2 ~ 4 மிமீ அளவு கொண்ட துகள்கள்.
3. நெகிழ்வான செயல்முறை ஓட்டம்: கலவை உர உற்பத்தி வரியின் செயல்முறை ஓட்டம் உண்மையான மூலப்பொருட்கள், சூத்திரம் மற்றும் தளத்தின் படி சரிசெய்யப்படலாம், மேலும் உண்மையான தேவைகளுக்கு ஏற்ப தனிப்பயனாக்கப்பட்ட செயல்முறை ஓட்டம் வடிவமைக்கப்படலாம்.
4. முடிக்கப்பட்ட பொருட்களின் நிலையான ஊட்டச்சத்து விகிதம்: மூலப்பொருட்களின் தானியங்கி அளவீடு, அனைத்து வகையான திட, திரவ மற்றும் பிற மூலப்பொருட்களின் துல்லியமான அளவீடு, முழு செயல்முறையிலும் அனைத்து ஊட்டச்சத்துக்களின் நிலைத்தன்மையையும் செயல்திறனையும் கிட்டத்தட்ட பராமரிக்கிறது.
Cஓம்பவுண்ட் உர உற்பத்தி எல்ineவிண்ணப்பங்கள்
1.சல்பர் பூசப்பட்ட யூரியா உற்பத்தி செயல்முறை.
2. பல்வேறு வகையான கரிம மற்றும் கனிம உர செயல்முறை.
3.அமில கலவை உர கிரானுலேஷன் செயல்முறை.
4. தூள் தொழிற்சாலை கழிவு கனிம உர செயல்முறை.
5.பெரிய துகள் யூரியா உற்பத்தி செயல்முறை.
6. நாற்று அடி மூலக்கூறு உர உற்பத்தி செயல்முறை.
இடுகை நேரம்: செப்-27-2020